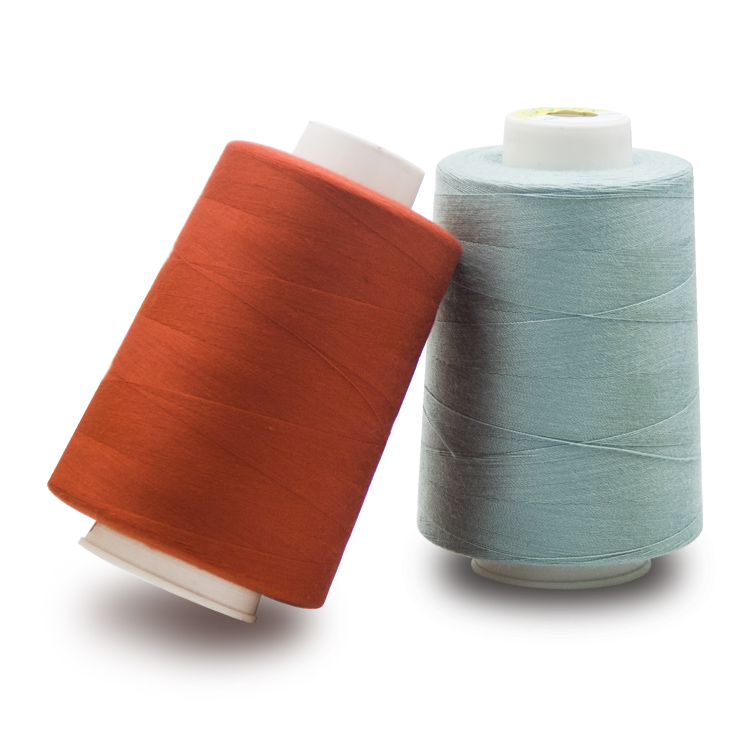
Basic knowledge of yarn hairiness(2/3)
The yarn hairiness problem has the following phenomena:
1. The overall value of hairiness is high and the fabric surface is not clear, which seriously affects the dyeing effect.
2. The CV value of feathers is high and the fabric surface is not smooth, which causes dyeing difference.
3. The dense hairiness of a few yarns results in the formation of cotton balls and neps in the weaving channel, which affect the end breakage and fabric quality.
Factors Influencing Yarn Hairiness
Hairiness is mostly produced during drafting and twisting of spinning frame, and the number of hairiness after winding is 2-4.5 times that of original yarn hairiness, which seriously affects the processing quality and production efficiency of the later process. Many textile enterprises have tried their best to solve the phenomenon of yarn hairiness, but the result is not so good. Following is a brief analysis of the factors affecting yarn hairiness:
I. The influence of raw materials on hairiness :the length, fineness, maturity, short fibre percentage and impurities of raw cotton will have a direct impact on hairiness during yarn formation.
The length and regularity of the fibers are good, the cohesion between the fibers and the fibers is strong, and the probability of hairiness formation is small. When the length of the fibers is short, the fibers can not be normally covered in the spinning process, so that one end of the fibers can be exposed outside the helix of the yarn body more opportunities to form hairiness; the impurities carried by the fibers themselves are more likely to form hairiness. Defects easily occur in the spinning process, which affect the normal operation and straightening of the sliver, and increase the chances of the fibers exposing to the yarn body to produce hairiness; the higher the short fibre rate of raw cotton, the more planktonic fibers and hairiness in the drafting process; the higher the maturity of raw cotton, the better the strength of cotton fibers, and the thinner the fibers are relatively. Uniform and long. The number of fibers per unit length of the yarn decreases and the fibre head decreases. Moreover, the length of the fibre head that may extend out of the yarn body decreases due to the twisting torque and friction between fibers. Therefore, the yarn body is smooth and the hairiness is less; when the micronaire value of each mark in the same batch of raw materials is different and the consistency is poor, the control force of the fibers decreases during operation, and hairiness is easy to produce. Therefore, in the daily production process, we should strictly control the quality of cotton blending and the use rate of recycling, so as to improve the consistency and stability of raw materials.
II. The influence of each stage of Front Spinning on Yarn Hairiness
The combined opening and clearing of yarn will also have a certain impact on yarn hairiness, requiring that the channel parts of each equipment should be clean and without burrs and hanging flowers (feathering due to scratching), and that there should be no burrs and hanging flowers on hitters, dust sticks and cotton delivery curtains, so as to reduce the scratch and damage to fibers; the sharpness of each card cloth should be high. Good, enhance carding efficiency, reduce the chance of short pile production, reasonable speed, distance and drafting configuration of cylinder, doffer and cover, further straighten the fibers, reduce the probability of hairiness formation. The blowing-carding process has a greater impact on the fibers, and more fibers are broken in the process of high drafting, which makes the yarn worse in wear resistance and more hairiness.
Combing section: Generally speaking, the hairiness of combed yarn is 30%-40% more than that of combed yarn. By combing process, a large number of short fibers in sliver are eliminated, and the straightening parallelism of the fibers is improved, so the yarn hairiness will be reduced.
In the process of combing preparation, attention shall be paid to reduce the phenomenon of sticking, increase the noil properly in combing, keep the top combing, cylinder and brush in good working condition, and the whole cotton conveying channel shall be clean and free of burrs.
Drawing section should pay attention to the distribution of drafting, to promote the stretching of hook fibers, thereby reducing the probability of hairiness formation, horn mouth can not hang flowers, pressure bar should be regularly checked to ensure good condition.
In the roving section, yarn hairiness will decrease with the increase of roving twist, and the more hairiness the roving has, the more hairiness the spinning will have. The hairiness of the yarn will also increase, and it should be kept clean in all places where sliver passes through, and there can be no hanging flowers.
The friction between plastic sliver barrel and sliver used in each section of front spinning is easy to generate static electricity, and the mutual exclusion and attraction between fibers and fibers. Some short fibers can not be normally coated to form hairiness. Plastic sliver barrel should be smooth and without burrs.