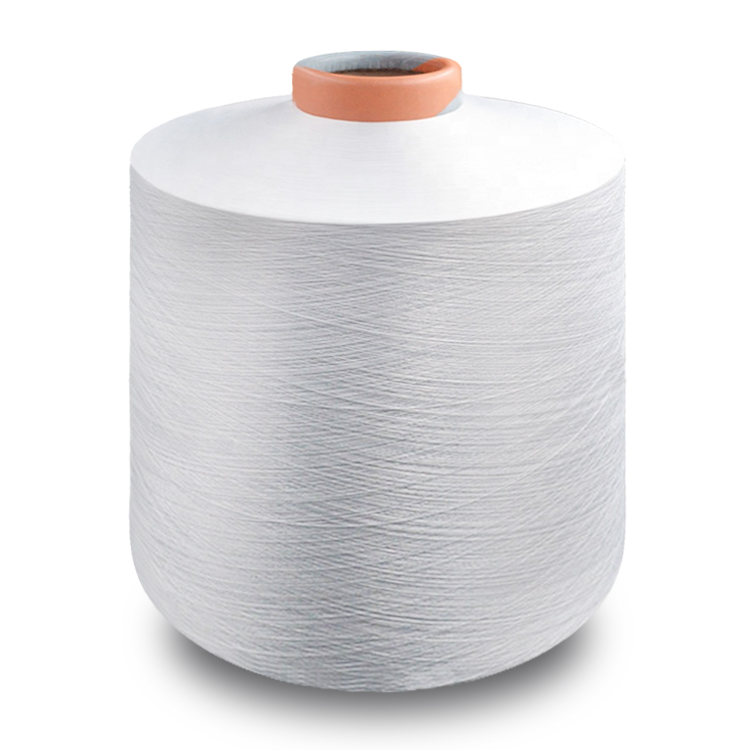
Cotton fiber without cotton: viscose fiber
Viscose fiber is a kind of chemical fiber with a long history, mature technology, huge output, various varieties and wide use. The regenerated cellulose fiber is made of natural cellulose (pulp) as the basic raw material, which is converted into cellulose xanthate solution and then spun.
Viscose history
Viscose fiber is one of the oldest chemical fibers, which is only later than cellulose nitrate fiber. In 1891, cross, Bevan and bedle first made sodium cellulose xanthate solution, which was named "viscose" because of its high viscosity.
After the viscose meets with acid, the cellulose is separated again. According to this principle, in 1893, it developed into a method for preparing chemical fiber, which was named viscose fiber. In 1905, Muller and others invented a coagulation bath composed of dilute sulfuric acid and sulfate, which realized the industrial production of viscose fiber.
The industrial production of viscose fiber has been one hundred years. In this one hundred years, the production technology has made continuous progress, from ordinary fiber to strong fiber and high wet modulus fiber. At present, the output of viscose fiber in the world accounts for about 12% of the total output of chemical fiber.
Since the 1990s, Europe, the United States, Japan and other industrial powers have shut down their viscose fiber factories and reduced the production of viscose fiber. They concentrated the production of viscose fiber in a few large companies, which is conducive to pollution control and the development of new technologies and new varieties.
At the same time, through technological innovation, they have greatly improved the quality of viscose fiber products, developed new varieties and technologies, and greatly improved the added value of products. For example, their viscose filament spinning speed has reached 140m / min, the size of the filament has been as thin as the thinnest silk, and hundreds of different fiber varieties have been developed, such as hollow, flame-retardant, deodorant, slub, alien, far-infrared, etc.
In terms of product quality, the dyeing consistency of viscose fiber is obviously improved, and the variation coefficient of hairiness and elongation is greatly reduced.
In addition, they continue to export new viscose fiber production technologies. For example, China's major chemical fiber companies are spending a lot of money to introduce their advanced technologies and equipment, such as continuous spinning machine, acid bath flash system, silk cake internal pressure washing equipment, waste gas recovery technology, etc.
Through the above measures, although the production of viscose fiber has been reduced in Europe, the United States, Japan and other countries, the labor cost has been reduced, the environmental pollution and treatment costs have been reduced, and the overall economic benefits have been greatly improved because of the substantial increase of the added value of its products and the large amount of technical output income [1].
The establishment of chemical fiber industry in China started from viscose fiber. Since the 1950s, China has successively established viscose fiber factories, such as Dandong Chemical fiber factory, Baoding chemical fiber factory, etc. In the past 50 years, viscose fiber has developed steadily. Since the 1990s, China's viscose fiber industry has developed rapidly, with an average annual growth rate of more than 10%. In 2004, China's viscose production reached 900000 tons, accounting for 1 / 3 of the world's total production, maintaining the position of the largest production country of viscose fiber.
Great potential
(1) Viscose fiber still has a bright future: viscose fiber itself has excellent dyeing, moisture absorption, anti-static and other properties, its fabric is comfortable, sanitary, natural and bright, with many kinds of properties that fiber can't, which is also the fundamental reason why viscose fiber is impacted by synthetic fiber and not washed out. With the improvement of the living standard of the domestic people, people's consumption concept of clothing and home decoration tends to "return to nature", and the ready-made clothing exports to the European and American markets are promising, which will correspondingly drive the growth of viscose fiber demand. Therefore, it can be predicted that viscose fiber will continue to be an important raw material for textiles. With the gradual withdrawal of developed countries from the production of viscose fiber, more market space will be given up, which is undoubtedly a historic opportunity for China's viscose fiber.
(2) Advantages of developing viscose industry in China: the production concentration of viscose industry in China is relatively high, the average production capacity of a single factory is more than 20000 tons, and some leading enterprises are close to the international level; the raw materials of viscose fiber are cotton pulp, wood pulp and other natural substances, and China's cotton linter (cotton pulp raw materials) resources are very rich, which can be obtained locally, which is very beneficial for enterprises to reduce production costs As the production of viscose fiber in developed countries is decreasing year by year, it provides space for the export of viscose filament in China.
Problems that cannot be ignored
Environmental protection problems: there are environmental pollution problems in viscose fiber production, mainly the pollution of hydrogen sulfide and carbon disulfide to the air and the pollution of organic matter and sulfate in wastewater to the water quality. Due to environmental protection reasons, developed countries gradually withdraw from viscose fiber production and transfer their production capacity to developing countries, among which China, India and Indonesia have the fastest development. If the traditional viscose fiber production measures in pollution control are reasonable, although the process is complex and the investment is large, the viscose fiber still has its vitality. The development of viscose fiber industry in China should not be at the expense of the environment. It is necessary to actively digest and absorb the latest achievements and successful experience of foreign viscose fiber manufacturers in the control of harmful substances emissions. The recovery rate of enterprises in developed countries is about 85%, and that of Lenzing's combined plant system is 90% [2].