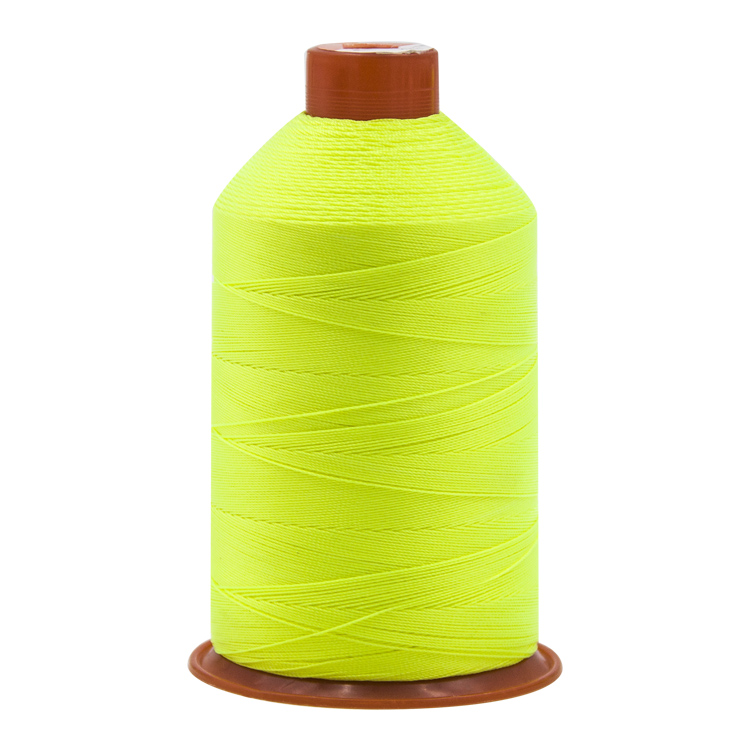
Number of return slips produced by the class
In the production management and cost management of textile mills, more attention is paid to the number of return slips produced in shifts, because it directly affects the cotton consumption coefficient and production cost of spinning mills, and directly affects the quality of cotton yarn and fabric. There are many factors affecting the return sliver: generally, the lower the grade of blended cotton, the worse the production environment, the worse the equipment operation and management, the more unstable the equipment status and spinning equipment quality, the worse the consistency, the larger the spinning number, the more the broken ends, the worse the air conditioning dust removal, the more the return sliver produced.
The production of the flyback is caused by the comprehensive factors of the spinning factory. Reducing its quantity is equivalent to reducing spinning cost, improving spinning quality and reducing labor consumption. This is the basis of all aspects of management of spinning plant to form a virtuous cycle, and it is also the key to reduce the fabric stripe defects, dead cotton white star defects, small NEP defects and small defects.
Causes and hazards of receipt
Sliver and cotton return are mainly found in the pre spinning process, which are related to blending control, packing control, equipment management, operation management, operation management and quality management. More than 90% of the returned cotton is produced by the difference of the packing height and the size of the mixed cotton, but the returned cotton is seldom caused by the operation quality and equipment failure. In many cases, equipment failure, quality accident and equipment test run will result in a large number of strands, which will not be treated or degraded in the spinning process, not only cause damage to carding elements, but also cause quality problems such as the increase of local neps of sliver, the increase of dead cotton and white stars of knitted and woven fabrics.
The packing position, density, height and the proportion of recycling will affect the operation management, equipment management, quality management, semi-finished product quality and final product quality of the spinning plant. The more cotton is returned, the worse the management of blowing process and blowing carding unit is, the more unstable the quality of blowing carding or blowing carding unit is, the more uneven the cotton is caught, the worse the mixing quality of mixed cotton is, the more serious the fiber is hit, and the more short fibers and harmful fibers are produced. Controlling the quality, quantity, density and shape of bales can reduce the quantity of cotton returned in the process of cleaning. The key to control the return of cotton is to have a uniform shape, a reasonable arrangement and a uniform height.
Common replies mainly include operation reply, quality reply, test reply, equipment failure reply, training reply, etc. The harm of sliver to spinning process is far greater than that of cotton. Because the sliver fiber has been loose, it is easier to damage the fiber in use, and the cohesive force between the fibers is worse, and it is easy to be pulled off, resulting in the increase of short fiber and harmful fiber. Reasonable control of the sliver in the pre spinning process is the main factor for the quality stability of semi-finished products and cotton yarn. The key to reduce the sliver is to strengthen the environmental management of the spinning plant, improve the proficiency of the pre spinning operators, reduce the equipment failure and prevent the drafting and looping accidents.
Among many kinds of slivers, the most dangerous ones are the long slivers from the head of coarse yarn and from carding to drawing. In the conventional carding to drawing process, it must be torn into a certain length of sliver that meets the recycling requirements, otherwise it will cause the beater and carding abnormal. However, the looping treatment of the coarse yarn head must be fully opened, otherwise a large number of harmful fibers will be produced in the use process, resulting in the increase of semi-finished sliver neps, cotton yarn neps, short and thick knots, and dead cotton and white stars in the fabric. Check the quality and reuse of the opening treatment of the coarse yarn head, on the one hand, it can make the coarse yarn head be used correctly, on the other hand, it can not only control the quality of the sliver, but also the quality of the cotton yarn and the fabric. In addition, we must attach great importance to the pollution of the recycled yarn, which can not be changed.
Causes and hazards of backflower
The quality of the flower is different because of the different spinning process. The spinning process is the process with the largest number of flyback.
The quality of common recycled cotton is worse than that of recycled cotton and sliver, and there are more kinds of sundries and pollutants, including a large number of coarse yarn heads, recycled heads, steel wire rings, paper scraps, rags, etc. the content of short fibers and hazardous fibers in recycled cotton is not only large in quantity, but also large in difference. When recycled, the quantity and proportion of recycled cotton shall be controlled, and the equipment can be kept in normal operation and reduced in grade It can prevent the defects of semi-finished products, cotton yarn and fabric from increasing; improper use of recycled flowers will not only increase the number of flying flowers in the workshop, increase the accumulation of embedded flowers in the equipment, but also cause the fluctuation of semi-finished products, cotton yarn and fabric, and also cause the fabric to produce dead cotton white stars, neps, horizontal bar defects, long and short details and thick sections, etc. The quality of mixed cotton, the state of equipment, the operation management and the poor production environment are the key reasons for the increase of backflower. It is necessary to control, use, classify and sort the return flowers in actual production.
Under the same conditions, the proportion of recycled cotton must be much smaller than that of recycled cotton and sliver, otherwise the quality of cotton yarn will deteriorate and the quality of fabric will not be controlled. Making clear the production, treatment, use and proportion control of cotton returning, sliver and flower returning can not only control the production cost of spinning, but also make