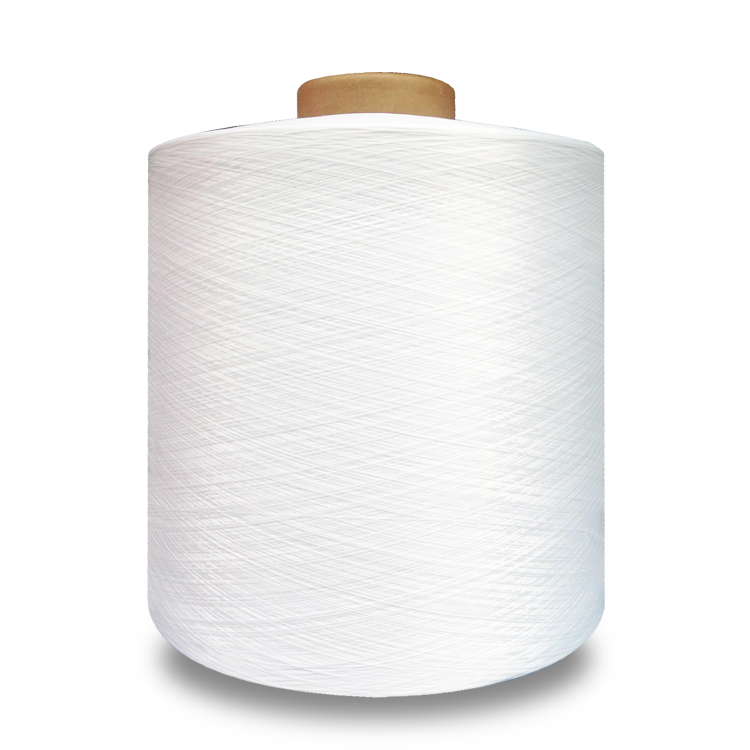
How to use yarn thread roving equipment (1)
The roving machine plays a key role in the textile yarn thread industry.
How to use roving equipment?
The author summarizes the following four practical experiences to share with you.
Quality control of yarn thread roving frame selection, installation and maintenance
1) Selection of yarn thread equipment: There are many roving machine manufacturers on the market at present.
There are more than ten different models at home and abroad.
Each manufacturer has its own advantages and disadvantages.
According to the variety, product grade and capital situation of the yarn thread manufacturers, we can choose the suitable yarn thread equipment model. The purpose of type selection must be achieved: not only to meet the production needs, but also not to waste enterprise funds, but also to ensure that the equipment is always in good condition.
2) Installation of yarn thread equipment: After selection, installation of yarn equipment is an important link to ensure yarn thread product quality, and is also the most basic work.
Those who have the ability to install yarn thread equipment by themselves and in poor condition, it is better to ask the yarn thread equipment manufacturer or the technicians with better technology to install and debug, and must find professional personnel to strictly check.
Sample in the future production, you can easily carry out the yarn thread production work.
3) Maintenance quality of yarn thread equipment: Carrying out daily maintenance of yarn thread equipment is the most basic daily management, the key is to complete, comprehensive, without leaving "dead corner", that is to say, to really maintain in place.
4) The purpose of yarn thread equipment maintenance is to ensure that the yarn equipment is always in good condition.
Control of yarn thread roving tension
1) To make the yarn thread roving winding smoothly on the roving tube, the winding speed of the bobbin must be slightly higher than that of the front roller, so tension and tension drafting are produced on the yarn thread between the front roller and the roving tube.
It is the key of roving production, which not only affects the roving life, but also directly affects the yarn thread quality.
2) According to the requirement of yarn thread spinning quality, the maximum elongation should not exceed 3%. It is advisable to control the elongation difference between yarns threads of the same machine size, between front and rear rows, and between machines of the same kind and machines below 1.5%.
3) The yarn thread from the front roller to the top of the spindle wing has a smaller twist due to the twist phenomenon and a longer distance.
At the same time, the spindle wing has a dithering phenomenon when turning at high speed, which is the most prone to unexpected elongation.
According to experience, it should be adjusted that when the yarn thread is winded from the starting point to the second layer at the bottom of the barrel, the yarn thread can shake slightly, but it is advisable to have no wave head.
If the upper yarn thread is tense, it means that the winding speed is too fast and the elongation is too large, the starting position of the taper pulley belt should be moved upward to the large end of the taper pulley, and no taper pulley should be controlled and adjusted from the frequency converter.
The ultimate goal is to achieve a consistent slight jitter state.
If the yarn thread is gradually tightened during spinning, it shows that the taper pulley belt moves too little at a time, the number of tension teeth should be reduced, and vice versa, the number of tension teeth should be increased.
4) The factors affecting the change of yarn thread roving tension are: Yarn thread roving quantity, front roller speed, twist, raw cotton quality, temperature, humidity and mechanical state.
Therefore, yarn thread roving quality account should be established in production, which is absolutely necessary to ensure production.
The size, difference and irregularity of yarn thread roving tension will affect evenness and weight irregularity of roving.
It is an important index affecting roving quality, so it should be strictly controlled.
Because the number of fibers in the yarn thread roving section is much less and the twist is lower than that in the spinning, it is easy to produce unexpected elongation, worsen the evenness of roving yarn thread evenness and increase broken ends after enduring greater tension.
5) When the tension difference is large, the weight irregularity of yarn thread roving increases obviously, which should be controlled within 1.0%.
When the roving tension is low, the formation of the yarn thread roving is loose and rotten, and it is difficult to store, transport and unwind, which affects the quality of the roving itself, and also increases the uneven weight and weight deviation of the yarn thread.
For example, when spinning pure cotton yarn thread roving on a roving frame with poor false twist effect, the quality index of the front row is inferior to that of the back row.
Under the same spinning conditions, the difference of front and rear row tension will result in quality difference.
Of course, under the condition of better false twist effect, the back yarn thread spinning tension may be greater than the front spinning tension.
Therefore, in the aspect of roving quality management, we should not only pay attention to the influence of drafting part on quality, but also grasp the change of roving tension.
Process control of yarn thread roving frame
The technological parameters of yarn thread roving frame mainly include: Ration, spindle speed, draft multiple, roller grip distance and apron nipper distance, roller pressure, twist coefficient, winding density, diameter of collector and bell mouth, and number of winding paths by pressing palm.
1) Yarn thread roving quantity is determined by drawing capacity of spinning frame, number of spinning yarns threads and product quality, and mainly by number of spinning yarns threads. The heavier the yarn thread is, the bigger the drafting ratio will be, and the yarn thread evenness will be affected.
Now there is an increase in the amount of 10 g/10 m, spinning to "V" drafting, yarn thread is also good, worthy of promotion.
In a word, the total drafting multiple of yarn thread roving frame should refer to the drafting form of yarn thread roving frame besides the number of yarns threads and the quantity of clinkers.
As the current development of yarn thread spinning frame towards high drafting multiple, yarn thread roving can be equipped with lower drafting multiple, which is beneficial to quality.
When double short apron draft yarn thread roving is used, the draft ratio can be slightly higher than that of three-up-four-down curve draft, generally 5-12 times.
2) Drafting distribution of yarn thread roving frame depends on drafting form and total drafting multiple.
When the yarn thread drafting capacity of main drafting zone is large, the drafting multiple of main drafting zone should be large.
Double-short apron drafting belongs to one of the larger drafting zone capabilities.
Practice has proved that, under the condition of constant sliver feeding and roving ration, the back yarn thread drafting multiple should be large.
The larger the number, the worse the yarn evenness.
Therefore, when the process conditions in the main yarn thread drafting zone are better, the lower the back drafting ratio should be.
(Not finished).