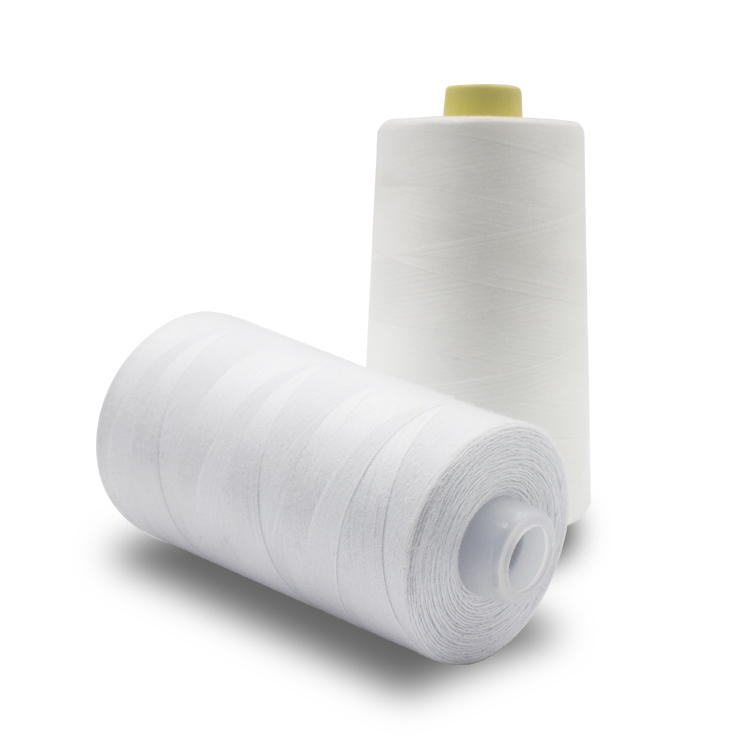
How to use yarn thread roving equipment (2)
(continued above)
3) Rear drawing ratio: Rear drawing ratio has a great influence on yarn thread roving evenness.
In general, the double apron yarn thread drafting device, because of the strong friction of the apron part, and has an elastic clamp, can stabilize the yarn thread drafting force, so that the fiber yarn thread speed change point forward, both concentrated and stable.
Therefore, the post-draft ratio is usually between 1.08 and 1.4 times. In production practice, we adopt 1.1 times rear draft and evenness of yarn thread roving yarn on A454, FA468E, FA458A and FA421 yarn thread roving frames.
Of course, the quality of the sliver is also related to the pressure of the apron roller.
When determining the post-draft multiple, we should first understand the slip rate of the middle roller of the lower apron, and try to reduce the slip rate of the upper and lower aprons.
In addition, when the weight of yarn thread roving is too heavy, in order to prevent the sliver from delaminating, a larger draft ratio can be chosen.
When spinning knitting yarn thread, in order to prevent the details of the long segment of the yarn thread, the draft ratio of the back zone should also be grasped on the small side in the case of choosing a smaller total draft ratio. For the three-up-four-down draft form, because of the anti-encircling arc on the third roller of the back zone, when the quantity of ripe sliver is relatively light, the draft multiple of the back zone should also be controlled on the small side, generally 1.17-1.36 times.
4) When using large package high yarn thread roving frame, the spindle speed can reach 1000 r/min to 1500 r/min, and the yarn thread roving quantity should not be too light.
Otherwise, unexpected yarn thread drafting will increase, resulting in more broken ends of roving and spinning, which is difficult to do in daily life.
5) Twist coefficient: When the fiber yarn thread is long, neat and fine, the twist number should be small, and vice versa.
Yarn thread roving has twist, so that it can withstand the tension in winding and unwinding, and is conducive to the control of the fiber yarn thread in the back zone of spinning.
However, if the twist coefficient is too large, not only the strength of yarn thread roving will be uneven, but also the spinning will produce cots skidding, hard ends and increase broken ends.
Conversely, if the twist coefficient is too small, unexpected drafting will occur, and broken ends will also be increased to make the products uneven.
6) Roller spacing and pressure: Roller spacing should be determined according to the length of the fiber yarn thread, too small damage to the fiber yarn thread, or even hard head, too large fiber yarn thread movement irregular, worsening the CV value of evenness and other quality indicators. Roller pressure is to ensure that the roller nipper has sufficient grip force, to prevent slippage and excessive stratification of the yarn thread under the roller nipper.
Whether the roller nipper can effectively control the fiber in the drafting process directly affects the evenness and weight irregularity of the yarn thread and the formation of roving defects.
On the yarn thread roving machine with spring rocker pressure, the spring swing top pin and step down pin apron nippers are used to control the nipper, and the original distance of the nipper is determined with the quantitative change of the yarn thread roving.
When quantifying more than 5 g/10 m, the original spacing of 4.5 mm, 5 mm, 5.5 mm and 6 mm should be selected.
Under sufficient spring pressure conditions, a smaller clamp should be used to make the product uniform, but the spring pressure should be regularly corrected.
If the pressure is not uniform, it will cause greater difference between ingots, and if the clamp is too small, it is easy to spit hard head. 。
7) The front zone and the middle zone collector of the yarn thread roving frame are also equivalent to an additional frictional boundary.
The caliber of the front zone should be suitable for the yarn thread roving quantity and the middle zone should be suitable for the ripening quantity.
8) The spindle has no pendulum head, which is controlled within 0.03 mm. The bending is too large, resulting in the increase of broken ends and irregular roughness.
9) The spindle wing should be balanced dynamically and statically, not skewed, smooth passage, proper pressing and loosening.
Over-tightening yarn thread can produce hairiness and easily fall off.
The arm opens big, collides with each other, while the arm opens small, it grinds yarn thread.
If the radian of pressing palm is not qualified, the yarn thread roving winding will be loose and uneven in quantity, and even defective products will increase broken ends.
In order to maintain the normal operation of the machine and reduce wear and tear, it is necessary to regularly correct the wiping.
Effect of yarn thread drawing force on process quality
Drawing force itself is not a technical problem, but it must be taken into account when yarn thread designing drawing process parameters. It is related to the following factors:
1) The relationship between yarn thread drafting force and yarn thread drafting multiple: when the drafting multiple is equal to 1, there is no relative motion between fibers, and the drafting force is equal to 0.
With the increase of yarn thread drafting multiple, the drafting force increases sharply.
Later, as the fibers yarn thread begin to slide, the drafting force increases slowly.
When the drafting multiple approaches the maximum, the drafting force reaches the maximum.
The maximum drafting force will change with the number of feeding, the roller gauge, the dense arrangement of yarns threads and the straightness of fibers.
2) The relationship between yarn thread drafting force and feeding roving twist. If the feeding yarn thread roving twist is large, the yarn thread drafting force is also large.
When the yarn thread drafting ratio is low, the drafting force of roving with different twists is close.
This is because when the yarn thread drafting ratio is large, the roving twist disbands and the twist effect is not significant.
3) The relationship between the yarn thread pulling force and the yarn thread pulling distance: When the pulling distance is large, the reduction has little effect.
If the pulling force continues to shrink, the pulling force gradually increases. When the distance is small enough, the pulling force rises sharply.
This is because the end of some fibers extends into the back pliers and increases the pulling force.
4) The relationship between yarn thread drafting force and the density of the sliver: If the density of the sliver is increased in the yarn thread drafting area, the drafting force will increase accordingly.
When the yarn thread passes through the collector, the friction between the fibers threads is also increased, so the smaller the opening of the collector is, the greater the drawing force is.
5) The relationship between yarn thread drafting force and fineness, length and straightness of fibers yarn thread: When the fibers yarn thread are thin and long, the drafting force increases because of the high friction resistance between fibers.
If the fibers yarn thread are in the state of curling and interlacing entanglement, the friction force is larger and the drawing force is larger.
On the contrary, the more straight and parallel the fibers yarn threads are, the smaller the drawing force is.
6) Relation with relative humidity of workshop. When the relative humidity increases by 10% and the drafting force increases by 8% in the range of 35%-75%, there will be a hard head when the relative humidity is very high.
The above is some experience of our company using yarn thread roving machine.
Correct use of yarn thread roving machine is a key part of textile engineering. Only by profoundly understanding the various connotations can we better use roving machine and spin high-grade products.