Cause analysis and solution measures of yarn thread cotton mesh breaking(2)
05 Aug / 2019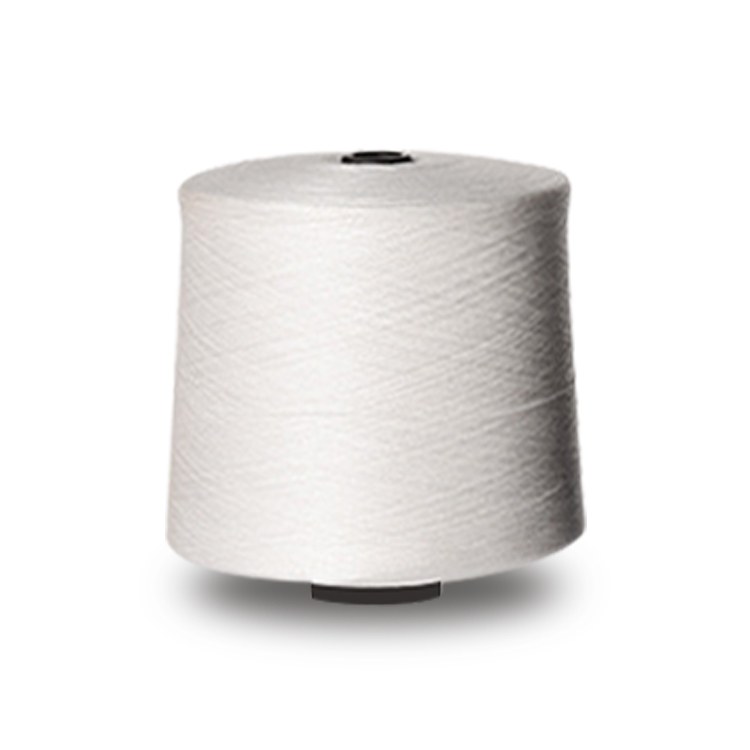
(continued above)
Cotton web hole
Yarn thread cotton web holes belong to the transverse unevenness of cotton web.
The yarn thread cotton webs with holes have a great influence on the uneven evenness and weight of the sliver on the surface of the car.
In the production of this kind of phenomenon, the machine should be stopped immediately for maintenance.
Phenomenon
When the separating yarn thread cotton web is conveyed from the separating pliers, there are holes of different sizes in the shape of cat's eyes.
Some of the yarn thread cotton web holes are quite regular, in each plier cycle; some are basically in the same position from the location of the rupture; others are irregular, only occasionally appear.
Broken yarn thread cotton web, the shape of its noodles will become hairy, wrinkled or have a significant uneven thickness and other adverse conditions. If the sliver is twisted by hand, the unevenness of the sliver can be detected immediately.
Yarn thread cotton webs are severely broken, and long fibers can also appear in the noil webs on the surface of dust cages.
Cause analysis
1) Yarn thread cotton web holes are periodic, each plier occurs, and when driving slower, yarn thread cotton web does not break, when the speed is normal, yarn thread cotton web holes immediately occur.
This situation is mainly caused by too much separation between the brush and the triangular airflow plate, which causes the overflow of airflow in the high-speed rotation of the brush and disturbs the separation of the joints.
2) If the broken yarn thread cotton web is always in the same place, it may be that the upper and lower lip of the pliers is seriously impacted with debris.
3) The breakage of yarn thread cotton webs, such as tearing and showing a breakage, or even breakage of about an inch long section, is mostly the result of the failure of separating pliers to hold the bundles effectively.
The factors of poor grip strength of separating pliers can also be analyzed from the following points:
The surface hardness of NBR separating cots is too high and the elasticity is poor, which reduces the clamping area of separating nippers to yarn thread cotton webs, and the holding force to fibers is correspondingly small.
The poor flatness of the surface of NBR separating cots, the eccentricity of the axis and the bending of the cots exceed the stipulation are also the main reasons for the failure of the separating cots to hold.
The diameter of the outer circle of the separation roller groove is significantly different in the same joint, or the roller is severely bent.
Separating roller or separating cot winding can not make the separating jaw occlude tightly and affect the grip.
Maintenance methods
1) Improving the hardness of yarn thread separating cots and increasing the clamping force of separating nipples are the main methods to eliminate cotton web holes.
Now some factories use cots whose hardness is less than 70 degrees.
2) Overlay the inner and outer yarn thread separating cots to check whether there is concave surface of the cots. If there is light transmission in the middle, it means that one or two of the cots are bent, they should be replaced immediately.
3) The air flow of the brush should be strictly controlled.
Especially, the air flow between the brush and the triangular airflow plate should not be separated too much, and it is generally appropriate to be tangent. If the air flow breaks through the yarn thread cotton web, the triangular air flow plate can be properly moved downward to ensure that the yarn thread cotton web does not break down.
4) Check the upper and lower lip for insertion of sundries or cotton wax, especially when processing cotton with high sugar content in summer.
Clean up debris or cotton wax on lips in time.
5) The surface of cots and rollers should be kept clean without burrs, so as to prevent the annular winding fibers. If it is found that the outer diameter of the separation roller groove is thick or thin, it should be changed in time and straightened in time when the separation roller bends.
Preventive measure
1) Separation cots should be regularly replaced and maintained to ensure the cots status.
2) Internal and external separation cots should be used separately (the quality of inner cots is higher than that of outer cots).
During the use of cots, regular grinding and eccentricity correction should be carried out, and corresponding handover procedures and assessment system should be established to ensure the quality of cots.
3) When the machine stops for a long time, the whole rubber roll should be released to prevent the deformation of the rubber roll.