How to save energy and reduce consumption in textile yarn thread enterprises
06 Aug / 2019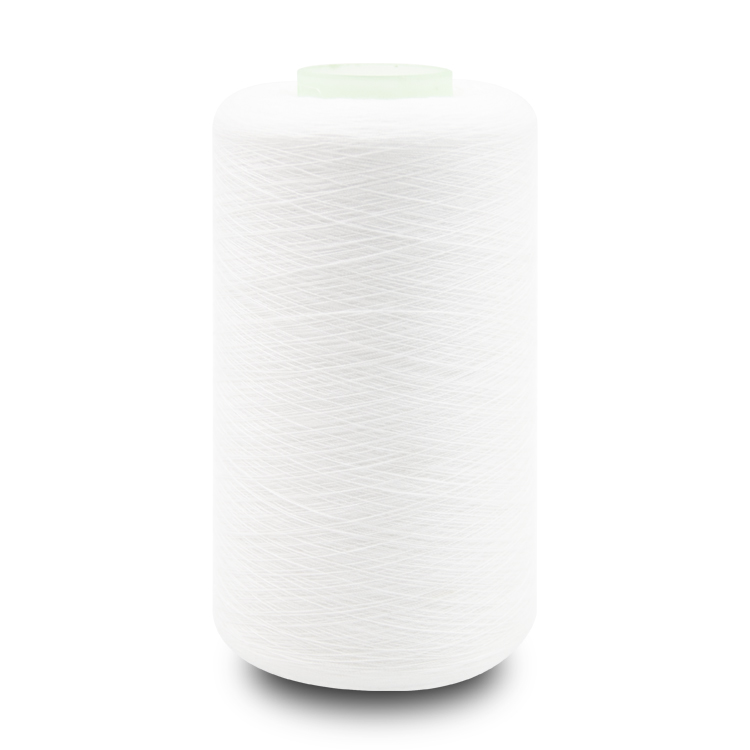
Textile yarn thread industry is a traditional labor-intensive industry with many production processes, high technological requirements, more labor and low profit. While improving product quality in the fierce market competition, more attention should be paid to energy saving and consumption reduction.
Yarn thread enterprises pay attention to management innovation and save employment
1. Yarn thread enterprises should merge,tape and reduce their institutions. Office automation, improve work efficiency, reduce duplication and ineffective labor. If the falling roving is hung directly on the spare hanging ingot or on the running hanging ingot, the labor of the intermediate link will be reduced. Equipment contracted, chartered to people, improve the employment environment. Implement fine rating, work at full load, and enhance staff's sense of responsibility.
2. Yarn thread enterprises should improve the automation and informatization of equipment. If the blowing-carding technology is used to eliminate the winding, the fine winding technology can reduce 2/3 of the yarn dropper, and the labor between the spinning and winding can be completely omitted. Generally, the automatic collective yarn dropping or intelligent yarn dropping trolley is used in the spinning frame to save labor.
3. Yarn thread enterprises should innovate operation methods and simplify operation procedures and technical requirements. For example, spinning joints should be replaced by "sleeve joints" to reduce technical difficulty. Electronic cleaning device on winder should be used to remove joints defects, shorten joints time, reduce staff training time, increase workers'stand and reduce labor.
4. Optimizing the process of yarn thread enterprises and using super-large drafting can not only improve the yarn quality level, but also effectively improve the unit yield of front spinning, achieve high yield and low consumption, and reduce labor.
Yarn thread enterprises avoid peak and valley, save electricity
1. Energy saving in yarn thread enterprise transformation, analysis, demonstration and transformation of high energy consumption links. Such as centralized suction of spinning yarn, broken end suction fan of spinning yarn, energy-saving spindle use, air conditioning system, clean intermittent work of blowing and suction air, etc.
2. Energy-saving management of yarn thread enterprises, power consumption index is decomposed into sections and teams, and measures are implemented to reduce empty spindles of roving, spinning and winding. Optimize the air flow rate of each process, use frequency conversion adjustment to eliminate the "big horse trolley", optimize the speed of each machine to achieve high production and energy saving.
3. Yarn thread enterprises process energy saving, to ensure output, yarn twist on the small side of support grip, optimize the process speed, increase output per hour.
Fourthly, policies should be adopted to save energy and make good use of the price difference between peak, Valley and level electricity.
The difference between peak and valley is 0.774 yuan/kW.h, which is a considerable economic benefit.
It is necessary to improve the energy saving of transformer power factor by "opening full valley, avoiding peak time and using peacetime reasonably".
Yarn thread enterprises should pay attention to the use of raw materials according to their quality
Yarn thread enterprises should carefully analyze the quality requirements of customers'orders, rationally mix cotton, and achieve quality standards, but not surplus.
At the same time, we should try our best to improve the production rate of each process.
1. Yarn thread enterprises should improve the use value of raw materials, reduce the recycling, control the recycling rate and recycling rate of each process, such as ensuring that the qualified rate of cleaning cotton winding is over 98%, controlling the recycling rate and recycling rate of carding cotton, controlling the roving head rate to ensure that the roving is not bad, controlling the number of remaining loops in the process of changing thread roving, controlling the recycling rate to ensure that the yarn thread is not broken, and controlling the recycling rate to ensure that the yarn is not broken.
Touch and grind rings to reduce bad yarn and ensure good spinning.
When winding, no tail yarn thread is left, and the clearing parameters are reasonably determined to effectively control winding return.
2. Yarn thread enterprises should economize on raw material cost and control the dropping rate of each process, such as controlling the dropping rate of opening and clearing cotton truck belly, diligently loosening, more miscellaneous and less white dropping; carding cotton should be more miscellaneous and less damaged fibers, more neps, control the growth rate of short staple, and ensure clear cotton web and good sliver. Combing ensures less noil, more rows of short lint and neps.
3. The yarn thread enterprises should rationally mix cotton and adopt process optimization measures to improve the execution ability of process level.